Bottleneck Queue Analysis and Recommendation on Adding Capacity
- lichutian
- Sep 20, 2016
- 2 min read
Challenges, Industry Trends and Sources of Variability
The main issues RP1 facing currently are the long wait-time for truck unloading, high overtime costs.
The secondary issue is that the Berries grading process at the receiving stage is inefficient.
Currently grading is conducted by chief berry receiver through visual inspection of the product which is leading to more than 50% of the lower quality berries being offered premium price of extra $0.5 per bbl. In year 1970 alone 225,000 bbls of low quality berries were paid premium price resulting in $112,500 loss.
The percentage of water-harvested berries will increase to 70% from 58%, this Industry trends would increase the pressure on cranberry wet process operations.
National Cranberry Cooperative subject to the variance such as, from macro perspective, the overall economic demand and factors that affect cranberry products like weather; also from operations perspective, such as truck arrival time, ratio of wet dry berry per arrival, qualities of the cranberries, labor availability.
Bottleneck Queue Analysis
Based on our assumptions
Wet-Dry ratio is 70:30
Plant, Truck has no break down or another interruption factor
No loss of berries during the process
Plant is ready to go at 7:00 am
current process flow chart

Demand
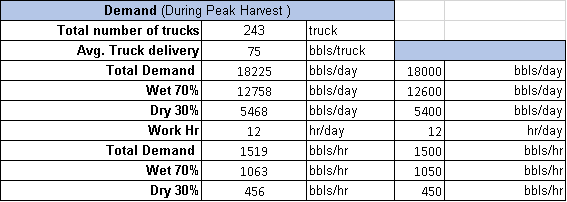
Capacity calculation
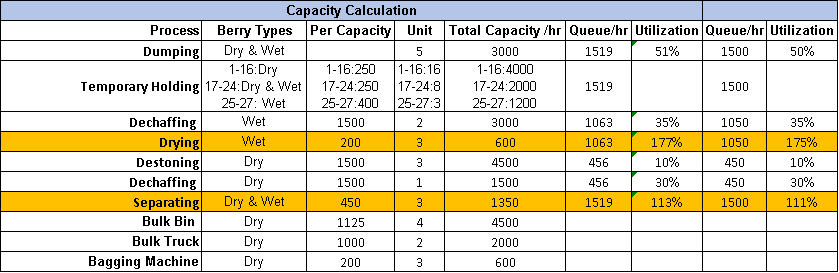
Therefore, Drying and Separating are constraints, while Drying is the bottleneck.

At capacity of 600 bbls per hr and demand of 1050 bbls per hr and 12 hr a day, the flow rate is 600 bbls/hr and 7,200 bbls/ day; With daily demand of 18,000 bbls, 70% being wet berry, National Cranberry is expecting 12,600 bbls wet berry per day, or 1,050 bbls per hour. Therefore, 12,600- 7,200 = 5,400 bbls will build up.
Assuming RP1 is ready to go at 7:00 am, the maximum capacity of the holding bins is 3,200 bbls, 5,400 – 3,200 = 2,200 bbls will be waiting and the time to process that is 2,200/600 = 3.67 hr. Truck driver will start to wait 7.11 hours after 7:00 am, which is 2:06:6 pm. The last truck driver will arrive at 7:00 pm and wait 3.67 hours till 10:40 pm.

Adding new Dryer
It helps! As mentioned above, drying wet berries is the bottleneck, adding additional will improve the process. And additional Dryer, with 200 bbls per hr, will increase the flow rate to 800 bbls per hr. Therefore, the number of bbls can be process will be 9,600 bbls and cumulated inventory will be 3,000 bbls, compared to 5,400 bbls. As shown in Appendix 6, adding new dryer can speed up 5 hours of the process.
Comments